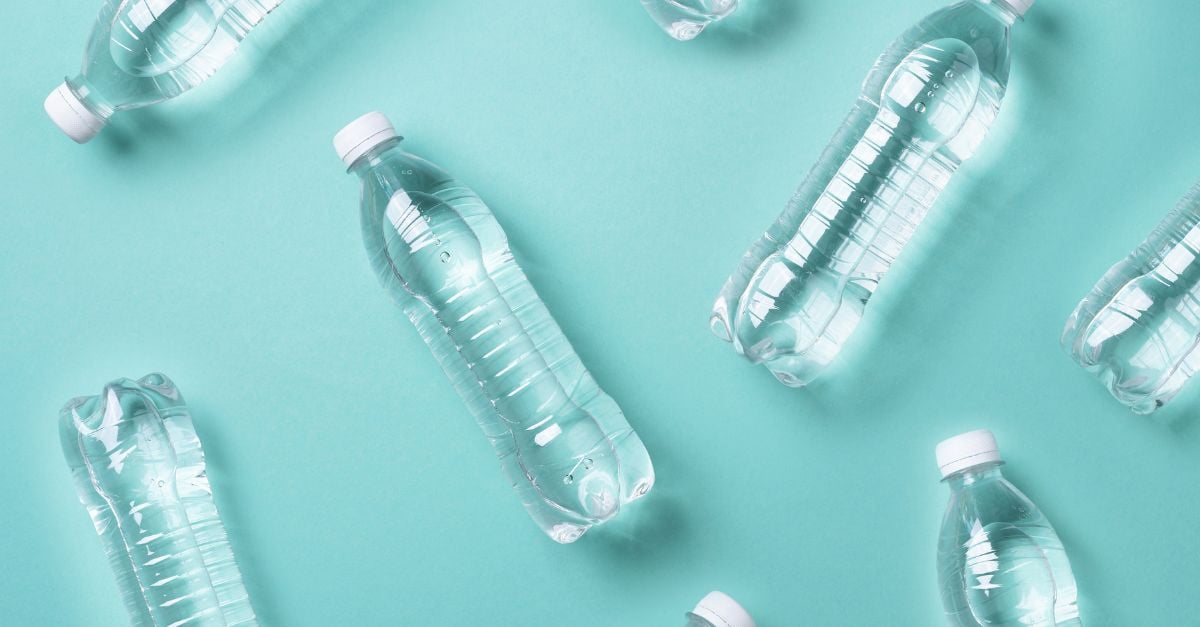
Using recycled PET plastics (rPET)
Overview of issues, market drivers and bottlenecks currently facing the recycled PET plastics market. We discuss the pros and cons of recycling PET plastics, what alternatives there are to obtaining high quality recycled plastics and much more.
Issues facing the market in relation to Mechanically Recycled Clear PET (rPET)
Everyone in the industry knows there are complex issues with regards to the availability, affordability and consistency of high quality clear rPET. There are so many factors that play into this that we wanted to showcase the different aspects to better understand this problem. We’ve also interviewed several brand owners, recyclers and other players in the market to get their perspective.
Table of contents
- Context: The pros and cons of recycling PET bottles and other plastic waste
- Background: Why is rPET so scarce and expensive?
- Costs: Factors driving up rPET prices
- The major hurdles of high quality rPET
- Different solutions to retain rPET value
- How does color neutralization work?
- The different forms of color neutralization for rPET
- See an example of colored rPET
- Case study: How one of the largest recyclers was able to create a steady supply of high-quality rPET
- Conclusion
Download this guide in PDF
Tip: you can always download this guide in handy, interactive PDF format.
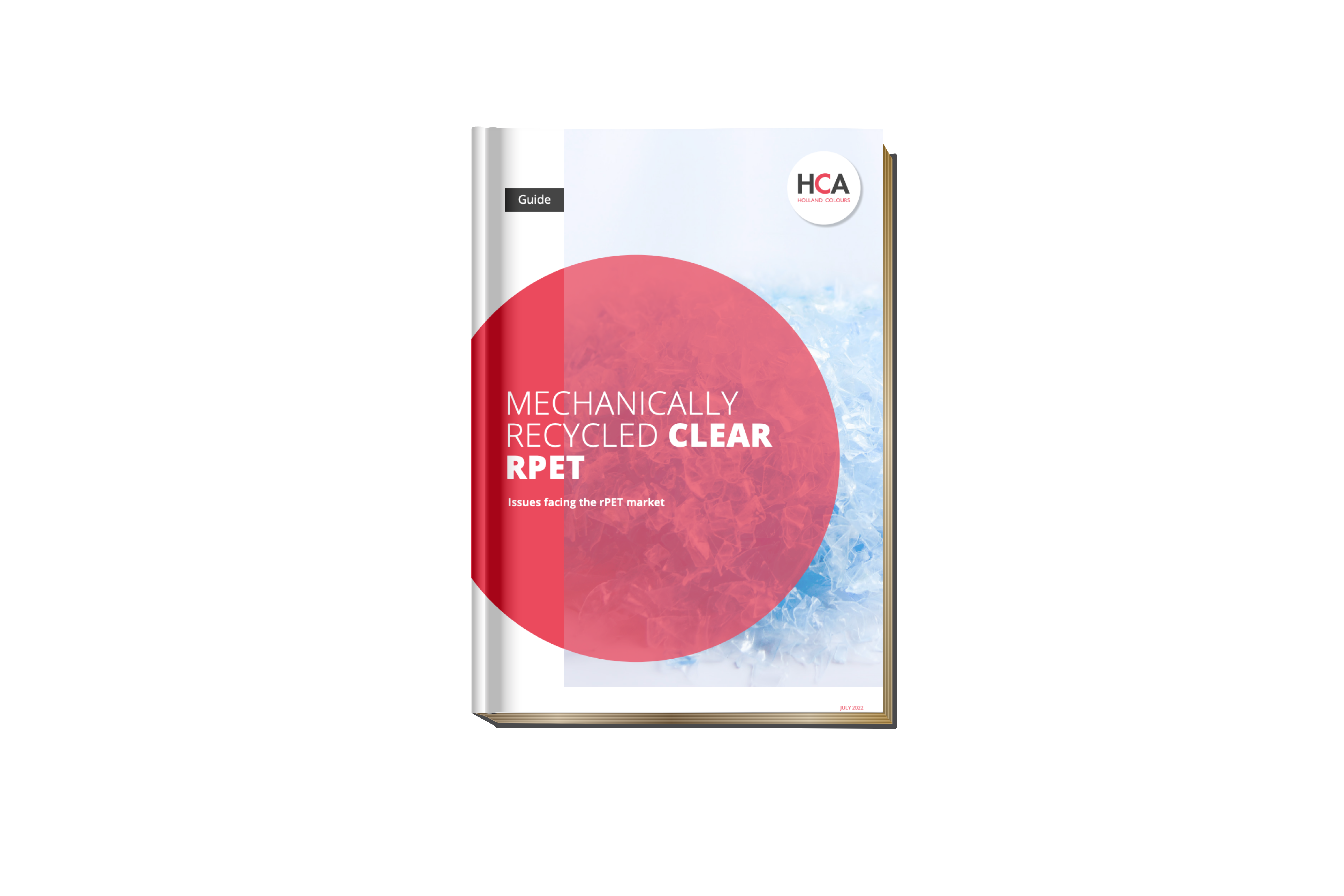
to stand
out
The pros and cons of recycling PET bottles and other plastic waste
Recycling PET plastics, for example in the form of rPET bottles, and other forms of plastics, has become very important over the last several decades.
Not only is recycling a more sustainable way of dealing with waste, waste, in itself, has also largely changed to becoming a valuable resource of raw materials, like rPET for packaging.
Before we dive in, here’s an overview of some of the most important pros and cons seen from our perspective as an innovator in sustainable colorants for plastics.
Recycled plastic is obtained either by melting used, sorted plastic - resulting in granulates- and turning these into new articles (mechanical recycling), like fiber for clothes.
Or by reverting it to its original building blocks and producing new plastic (chemical recycling). In both cases, much of this material comes from used items, such as plastic bottles, containers and so on that have been collected by consumers, retailers and waste deposit schemes.
The pros of recycling polyester (PET) and other plastics:
- Recycling prevents plastics from being incinerated, or going into landfill or ending up as marine litter. This matters because, in some estimates, if we keep dumping plastic at our current rate, in 30 years there will be more plastic than fish in our oceans.
- Recycled PET (rPET) is as good as virgin polyester and its production requires significantly less energy. Next, CO2 emissions are 50%, or even less, compared to regular polyester.
- Recycling reduces demand for crude oil and natural gas and reduces emissions from incinerators.
- The potential uses of recycled plastic, and rPET in particular, are growing. Existing applications: bottles, sheets, clothing and much more.
- Recycling plastic creates jobs and helps to drive innovation in recycling.
- Chemical recycling, unlike mechanical recycling, has the potential to make plastics infinitely recyclable without any loss of performance.
- Different plastics can be repurposed for different applications, such as textiles, insulation, chairs and benches, and so on.
- Governmental pressure in legislation is increasing. In 2025, 50% of all plastic must be recycled in Europe. Changing the design of plastic products and their packaging could increase the recycling opportunities enormously.
The cons of recycling polyester and other plastics:
- Mechanical recycling, which involves washing, shredding and melting used plastic, weakens that plastic over time and can result in discoloration (yellowing). In the case of rPET, the lower mechanical strength is compensated in both the recycling process and with the addition of Virgin PET in the use phase.
- Chemical recycling returns a waste plastic product to its original small molecules (monomers) or small fragments. These are indistinguishable from the ones used in virgin plastic production and can be fed into the regular polyester manufacturing system. But chemical recycling is a more expensive process than mechanical recycling.
- Recycled plastic used to create textiles releases microplastics when washed. These microplastics reach the oceans and cause pollution.
- Some people argue that recycling plastic blinds us to the real problem – the use of plastic, most of which does not get recycled, either because of a lack of technology, infrastructure or economics.
- Coloring is a challenge when recycling PET due to the variability and impurities in the recycling feedstock. This makes it hard to keep color consistent between batches.
Background: What is rPET and why is it so expensive?
rPET is recycled PET. It is what is made after the initial PET product (usually packaging) is used by the consumer after which it is collected to be recycled. The used PET is then processed in a recycling plant, decontaminated and turned into rPET suitable for indirect food contact, often times in the form of pellets or flakes.
All Food Contact grade rPET recycling operations have to have an EFSA approval. So basically rPET packaging, such as rPET bottles is simply PET that has been turned into rPET, fit for food contact.
While virgin PET is clear, recycled PET comes in a variety of color shades and corresponding prices. These color differences are caused by remainders from their previous life influencing the value of the recycled material.
The clearer the recycled plastic is, the higher the value and the higher the price – to the point where high quality rPET is often more expensive than virgin PET. The result is that it can make more sense for processors and brand owners to use higher levels of virgin PET simply to remain cost competitive.
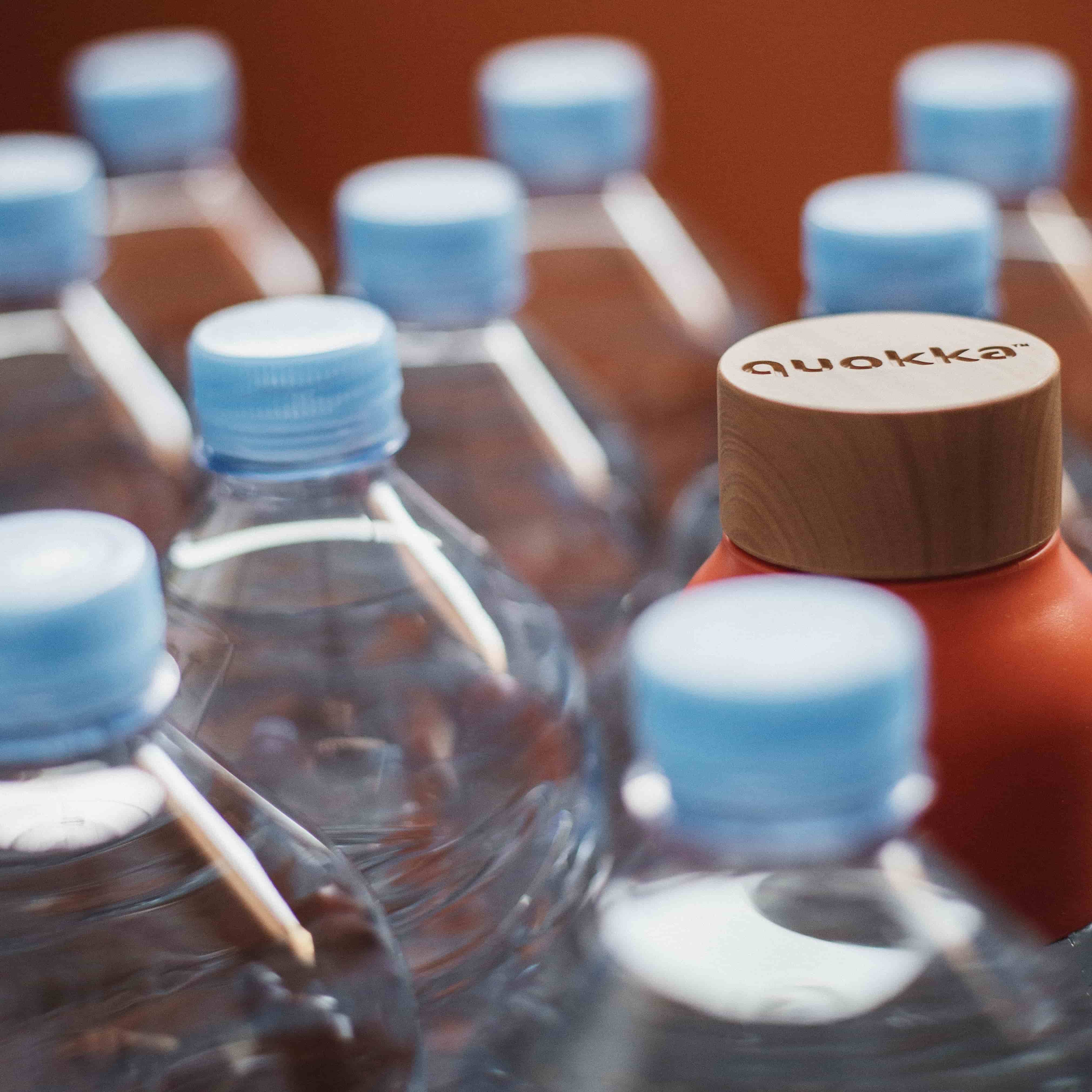
Factors driving up rPET prices
The reality is that high quality clear rPET is expensive. To fully understand why this is, it’s important to understand some of the underlying mechanics driving up the price.
New Regulations
There are new European regulatory requirements that mandate that as of 2025, PET bottles must contain on average 25% rPET. This means that in the European Union, these new requirements are creating a massive demand for high quality rPET in order for brands to be able to continue to sell in this region. In the Americas similar drivers are arising.
Below is an overview of some of the regulations:
- The EU has mandated the industry to include 25% recycled content in PET bottles by 2025 and 30% in all plastics bottles by 2030 under the Single-Use Plastics (SUP) Directive.
- Likewise, in the US state of California, manufacturers are required to include an annual average of 15% PCR in beverage containers starting in 2022. By 2025, the mandate is set to increase to 25% and by 2030 to 50%.
- Washington state has also recently announced a schedule for post-consumer recycled (PCR) requirements for different product categories, starting with beverage containers and trash bags in 2023, adding certain household cleaning and personal care products in 2025, and expanding to dairy milk containers in 2028.
Source: PackForward | Laws and regulations
Commitments Of Global Brand Owners
We’re also seeing a large push from brand owners who are moving in the direction of rPET packaging (like rPET bottles) independently and setting even higher targets for themselves than the 25% rPET content.
So beyond the initial demand, these goals for even higher percentages of rPET are driving up demand even further. It is up to the market to develop suitable solutions the address this increasing demand and avoid transitions to alternative, less desirable packaging materials.
Varying Quality rPET
The quality of mechanically recycled rPET can vary greatly. The quality is influenced and impacted by several different factors like the effectiveness of sorting and contamination. This means that there is a high demand and poor availability of high quality, clear rPET, the cost of rPET is sky-rocketing.
Costs: Conclusion
These factors all contribute to a massive demand for high quality rPET for rPET packaging. The industry is putting a lot of efforts on making more high quality rPET available through better collection, separation, sorting, washing and reprocessing.
We’re witnessing a shift in terms of food contact rPET purchase strategy. Brand owners have actively sought out ways to secure a steady supply of rPET that meets their standards by investing in and widening the Deposit Return Schemes and reprocessing facilities.
This ensures a steady flow of rPET which can be collected and processed according to their standards. More recently integration, consolidation and expansion of recycling capacity in the value chain has become the standard. But high quality rPET is still scarce. In order to hit the 25% rPET mark for PET bottles, concessions in quality of mechanically recycled rPET most likely have to be made.
Now obviously there can be no concession in food contact safety, but there are other alternatives to ensure a steady supply of high quality rPET. But what factors diminish the quality of rPET in the first place?
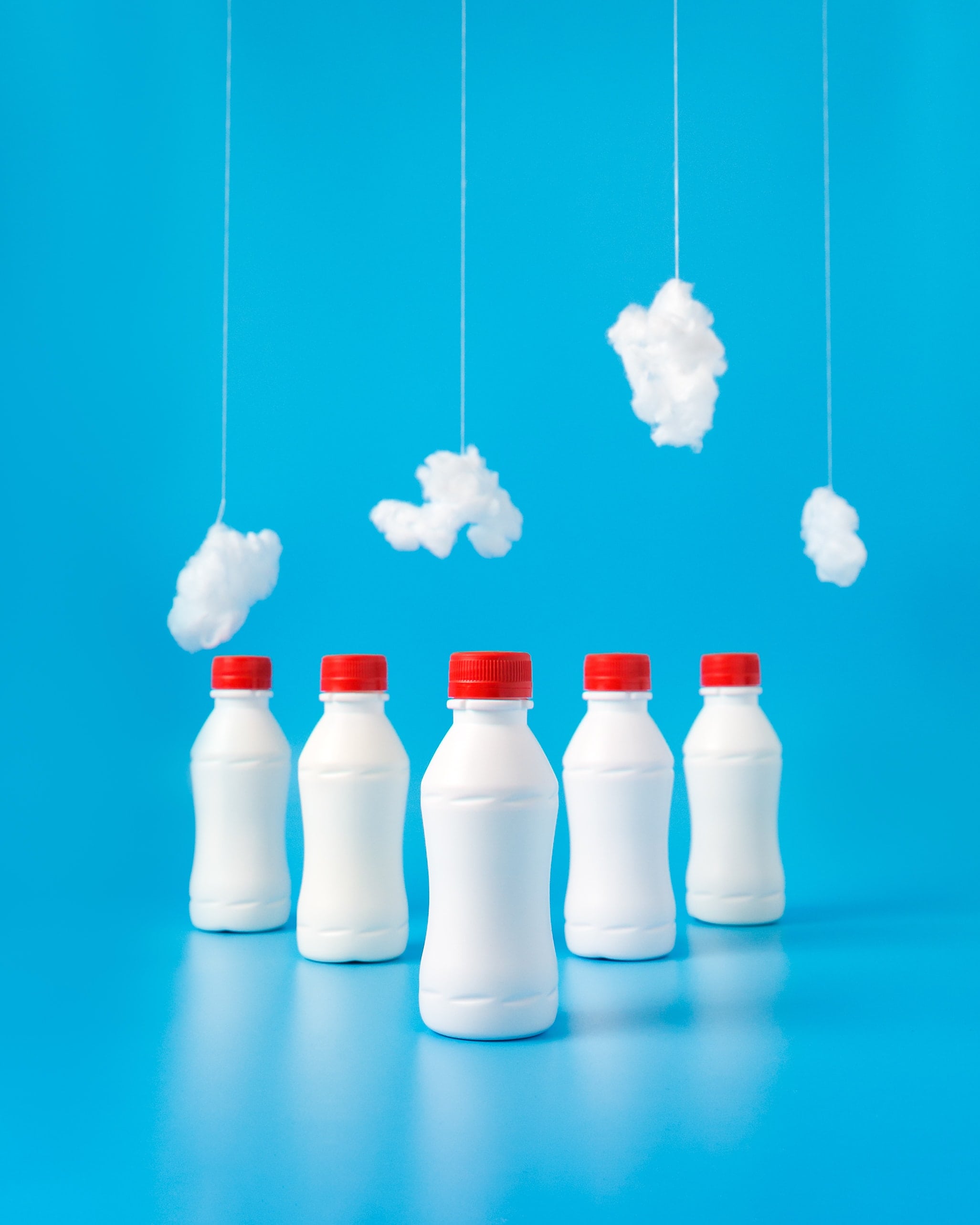
The Major Hurdles Of High Quality rPET
Consistency
One of the biggest hurdles when it comes to the visual quality of rPET has to do with its consistency. But what factors play a role in the lack of visual consistency of rPET? One of the biggest hurdles is the discoloration: After recycling, most of the time rPET experiences yellowing or other slight discolorations.
Discoloration
Undesirable discoloration of rPET during reprocessing is predominantly caused by remaining trace amounts of components like functional additives, colorants, adhesives, inks and other plastics from caps, labels and sleeves. Multiple heat cycles combined with residual component traces result in a higher level of discoloration. Hence it is key to ensure adequate washing and decontamination of the input material before reprocessing.
Effects
These are by themselves in many cases harmless and do not affect food contact safety but are undesirable due to their negative effect on color. This aesthetic deviation has proven to be unattractive for end-consumers.
Yellowing
This is quite understandable: drinking milk from a somewhat ‘yellowish’ transparent bottle feels strange for consumers who equate this color with a lack of hygiene and find it unattractive. During our interviews both the converters and brand owners seem to agree that a yellowish off-color is not accepted by the average consumer because it is associated with spoilt product.
Other aspects related to rPET quality are Intrinsic Viscosity (IV), absence of black spots
and haze.
What does the market say?
“In our interviews with converters, they’ve often stated they see the color cast of incoming rPET changing more and more. Moreover, consumer as well as market perception of a changing color cast of beverage bottles is inevitable. The expectation from brand owners is that in time the color-cast will be associated with sustainability. However, we’re not there yet.”
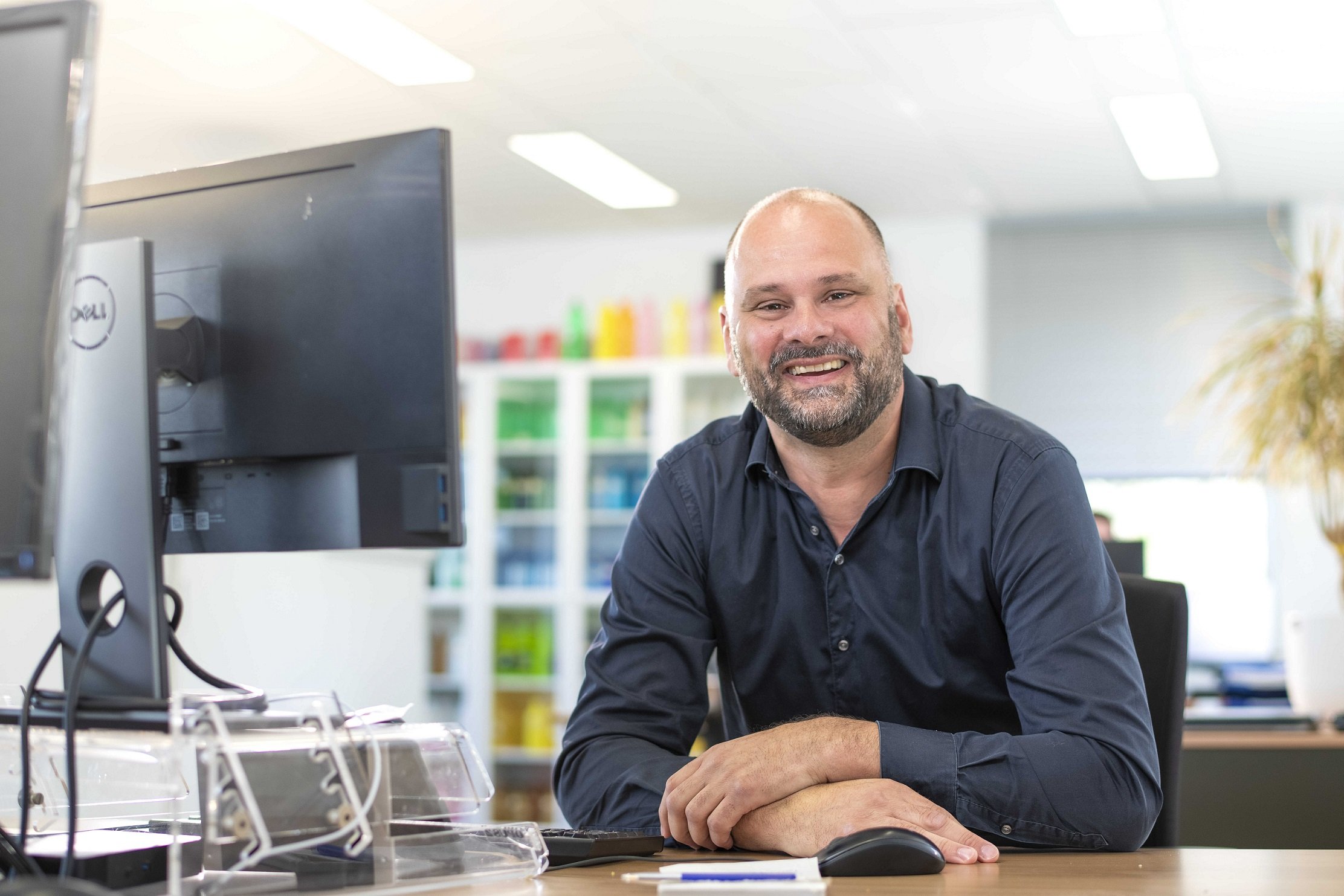
Different Solutions To Retain rPET Value
It is a given that high quality, transparent rPET is scarce and prohibitively expensive to come by. There are several options being worked on to address the problem of limited availability of high quality rPET. Most of these are clearly described in the Design for Recycling Guidelines by the various recycling platforms and associations. A solution that has already been implemented on a wide scale is to use completely clear packaging.
Eliminating color
Eliminating color in packaging will ensure that the value is retained. Reason being that packaging materials are predominantly separated in two recycling streams, I.e. clear and colored. Mixing and reprocessing various colors, even transparent versions, results in a lower quality output. As stated before the discoloration of clear rPET is due to multiple heat cycles in combination with residual component traces.
Closed loops
Another solution has been to use closed loops in the recycling process. For example, large brand owners own a stake in deposit return systems for PET bottles. This helps to ensure the quality of the PET bottles being collected and it allows them to standardize a significant portion of the PET collected for the recycling. This can help in some ways, but inevitably, after multiple heat cycles the same undesirable discoloration issues might arise.
Color neutralization
A technical solution to the undesirable yellowish discoloration is Color Neutralization. Using opposite colorants allows for a wider color range of rPET to be used, which of course means that while the total amount of rPET stays the same, more of the available rPET can now be utilized.
How Does Color Neutralization Work?
What Are The Different Product Forms And What Are Their Pros And Cons?
An undesirable color cast can be neutralized by means of adding an opposite colorant in the melt processing step, among others the extrusion and injection molding process. It is comparable to how noise-cancelling headphones neutralize sound coming from outside:
“[…] by using microphones to pick up low-frequency noise and neutralise it before it reaches the ear. The headset generates a sound that’s phase-inverted by 180 degrees to the unwanted noise, resulting in the two sounds cancelling each other out.”
The melt processing step could take place at a recycling facility but also at a (packaging) converter. By addition of the right amount of opposite colorant the rPET will be as close to virgin PET as possible from a coloristic point of view. However depending on the starting value of the input material, the L-value will always be affected.
Why color neutralization for rPET is so effective
“Opposite colorants used for optimizing rPET color are preferably pre-dispersed and encapsulated in a carrier material resulting in a concentrate or masterbatch allowing for economical and efficient dosing and dispersion in the final product. This solution offers enormous flexibility and can help create a reliable and consistent stream of high quality rPET that matches customer needs. These solutions are paramount in order to meet global sustainability needs.”
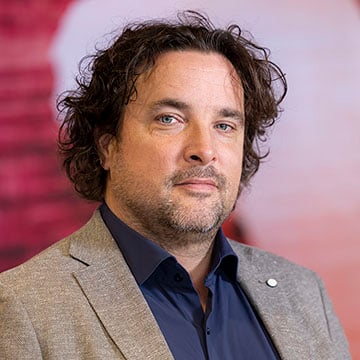
The different forms
Liquids
These concentrates are available in various product forms, depending on the type of carrier used, liquid or solid. A liquid concentrate allows for a low dosing rate also called let down rate (LDR). It’s easy to control and dispersed effectively in the target plastic. However it might have some stability issues with functional colorants or additives settling out. Furthermore some housekeeping challenges might occur when spilled.
Solids
A solid concentrate or masterbatch might be based on a wax or polymer and allows for cleaner and easier handling and depending on the type of carrier material either disperses very easily or requires somewhat more melt mixing shear. The colorant, carrier material and LDR of a formulation can be tailored to specific needs. Seeing as there is a trend towards 100% rPET, a wax based solid masterbatch might be preferred.
From a sustainability perspective, a non-petroleum, non-food source based wax based solid masterbatch is an excellent option which helps in the goal towards 100% rPET.
Also regulatory requirements in relation to the end-use have to be considered in the composition of the concentrate or masterbatch. The optimal specific product form depends on several factors like the needs and production setup.
.png?width=1500&height=750&name=Ontwerp%20zonder%20titel%20(4).png)
.png?width=1500&height=750&name=Ontwerp%20zonder%20titel%20(3).png)
How one of the largest recyclers was able to create a steady supply of high-quality rPET
How switching to TintMask® ensured stability and consistency
A company involved with the recycling of clear PET, one of the largest recyclers in Europe, contacted us. Like many others, they were experiencing difficulties in creating a consistent stream of high quality clear rPET for the converters further down the value chain. We have a full case study available, if you're interested.
Conclusion
We hope you’ve enjoyed reading this quick overview of the content. If you are interested in finding out more about how we can help you with neutralizing the undesirable color cast of clear rPET in a cost effective manner to ensure you have reliable and consistent supply of high quality rPET, please reach out to us here. We’d love to talk to you about our solutions so we can be of service.
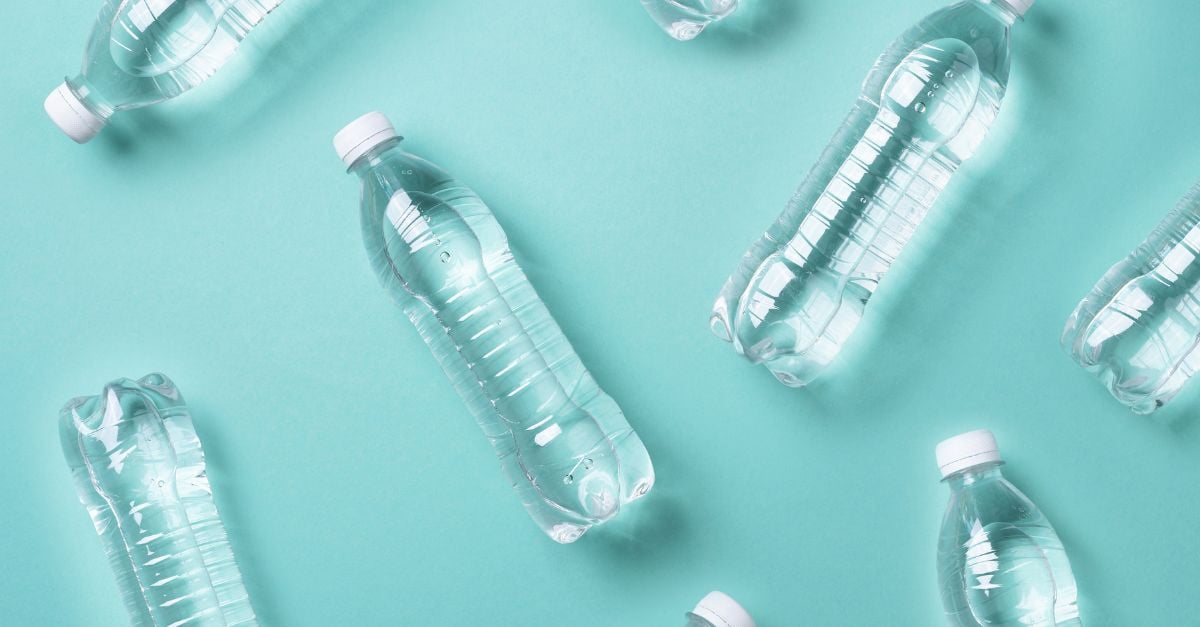